Engineer to Order (ETO) is a unique approach to manufacturing in which products are designed and fabricated according to individual specifications. Unlike more standardized manufacturing processes, ETO can be used to meet very specific demands.
However, this flexibility for customers comes with challenges for the manufacturer. Complex project management flows, intricate design requirements, and the even greater need for clear communication mean there are many opportunities for an ETO project to get derailed. This is where Product Lifecycle Management (PLM) systems can help create clarity.
Engineer to Order and Product Lifecycle Management
Product Lifecycle Management (PLM) systems like Siemens Teamcenter help the ETO process by providing much-needed clarity as a single source of truth that also creates greater governance. Teamcenter is a platform designed to manage every stage of a product’s lifecycle—from initial ideation and design to production and retirement. By integrating all aspects of the product’s lifecycle, the platform ensures that every stakeholder works with the most up-to-date information, which helps reduce errors and improve efficiency in ETO manufacturing projects.
ETO projects typically involve multiple departments, from Design and Engineering to Manufacturing and Quality Assurance. Siemens Teamcenter can connect these departments (and often external manufacturers or raw material suppliers) to keep everyone on the same page regarding design expectations, ownership, and deadlines.
This single source of truth for information decreases the likelihood of errors and misunderstandings. For instance, the Design team can work closely with the Engineering team to ensure the specifications are accurate, while the Manufacturing team can provide input in real-time on feasibility—all through Teamcenter. This collaborative approach speeds up the process and improves the final product's quality.
How does ETO differ from other manufacturing processes?
Engineer to Order manufacturing sits at the top of the tree when it comes to customization. However, other manufacturing processes better suit specific companies and industries because of different demand curves and consumer behavior.
Make to Stock (MTS): With the Make to Stock process, products are manufactured based on forecasted demand and stored until sold. MTS is an efficient way to sell standardized products but lacks the customization that ETO offers. MTS is commonly used for consumer electronics products like smartphones, packaged foods, and clothing.
Make to Order (MTO): MTO products are only manufactured after an order is received, which reduces inventory costs. However, these products are generally standard designs with limited customization. Furniture manufacturers and industrial machinery makers often employ MTO processes in their business models.
Configure to Order (CTO): CTO allows customers to select from pre-defined options and components, offering more customization than MTS or MTO but still within a limited framework. Computers, new vehicles, and even some kitchen appliances can be configured with a specific color, fabric, or engine for consumers who have certain preferences.
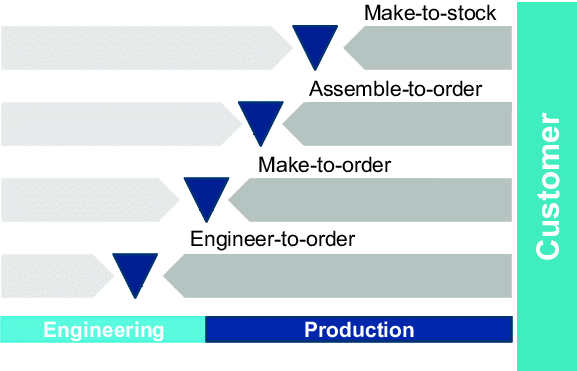
ETO projects customization with CLEVR and Optime Subsea
PLM systems are designed to make the overall management process far smoother. Siemens Teamcenter handles everything from managing customer requirements and design specifications to the coordination between different departments involved in the project.
Companies like Optime Subsea specialize in ETO manufacturing, delivering the equipment needed to drill for oil and gas at eye-watering depths. This means engineering specifications and manufacturing must be aligned perfectly—anything that even slightly deviates from the requirements could be unusable due to the dangers of deploying machinery at such depths.
CLEVR helped Optime Subsea create a roadmap to implement Siemens Teamcenter, helping to organize existing files, CAD vaulting, and access issues. This represented Level 1, which focused on Product Data Management.
Level 2 highlighted the need for serialized structures and general Process Data Management. Serialized structures were established thanks to information from different sources collected in Teamcenter, making it easy for Optime Subsea to differentiate between each project by its specifications. This was especially important for two reasons: Firstly, although Optime Subsea manufactures equipment that broadly serves the same projects—namely deep-sea wells—each project requires slightly different specifications, so making sure these requirements are easily distinguishable is crucial. Secondly, because of the risks associated with deep-sea drilling, the equipment must have clear and auditable material sourcing information to maintain the integrity of Optime Subsea and the industry in general.
Serialization, brought about by PLM as a single source of truth, also allows for the accumulation of records of manufacturing and design, as well as the fulfillment of manufacturing (e.g., welding logs and certificates of conformity). Being able to edit and check against these records while ensuring everything is updated in real-time is key when looking to service pieces of equipment before redeployment or when starting a similar project that meets many of the same requirements. With Teamcenter, these changes can be managed easily, with all stakeholders updated in real time to ensure everyone is on the same page and the project progresses smoothly.
ETO Project management with Siemens Teamcenter and Easy Plan
Project management with Siemens Teamcenter is designed to handle the complexity of ETO projects that involve multiple stages and stakeholders. When a change in customer requirements forces a product redesign, Teamcenter’s tools, which include Easy Plan, ensure that these changes are managed smoothly. Easy Plan simplifies the creation and management of production plans by linking product and process data, enabling real-time updates and collaboration. This seamless integration ensures that all stakeholders remain informed and aligned, allowing the project to progress efficiently while maintaining consistency across the entire lifecycle.
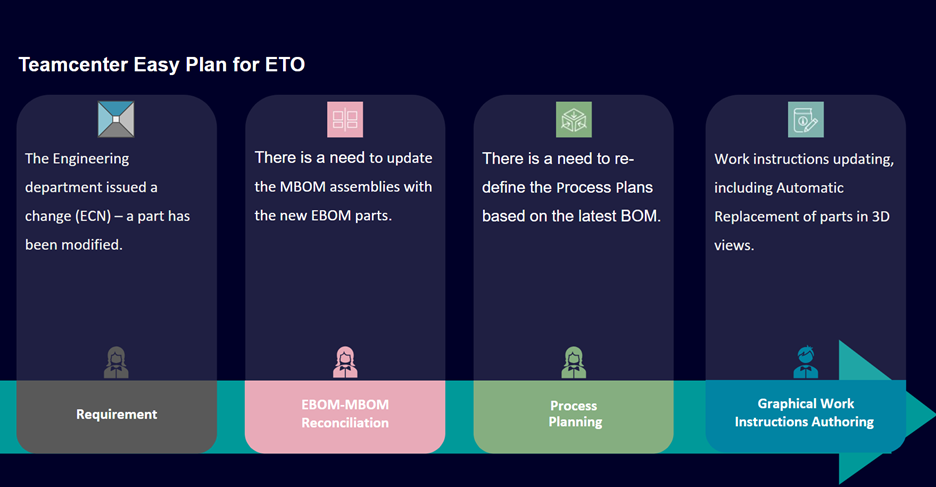
CLEVR
CLEVR delivers digital transformation at scale by implementing Siemens and Mendix solutions to serve industries like manufacturing, retail, energy, and more. We leverage PLM, MOM/MES, and low-code technologies for manufacturing optimization and business process automation while ensuring seamless integration with other core systems like SAP, IBM, and Salesforce. CLEVR brings together technology and industry expertise to provide strategic solutions that streamline operations, drive efficiency, and enable digitalization to fit market demands.
Find out how CLEVR can drive impact for your business
FAQ
Can't find the answer to your question? Just get in touch